DX(デジタルトランスフォーメーション)
経済産業省が定める「DX認定事業者」に認定
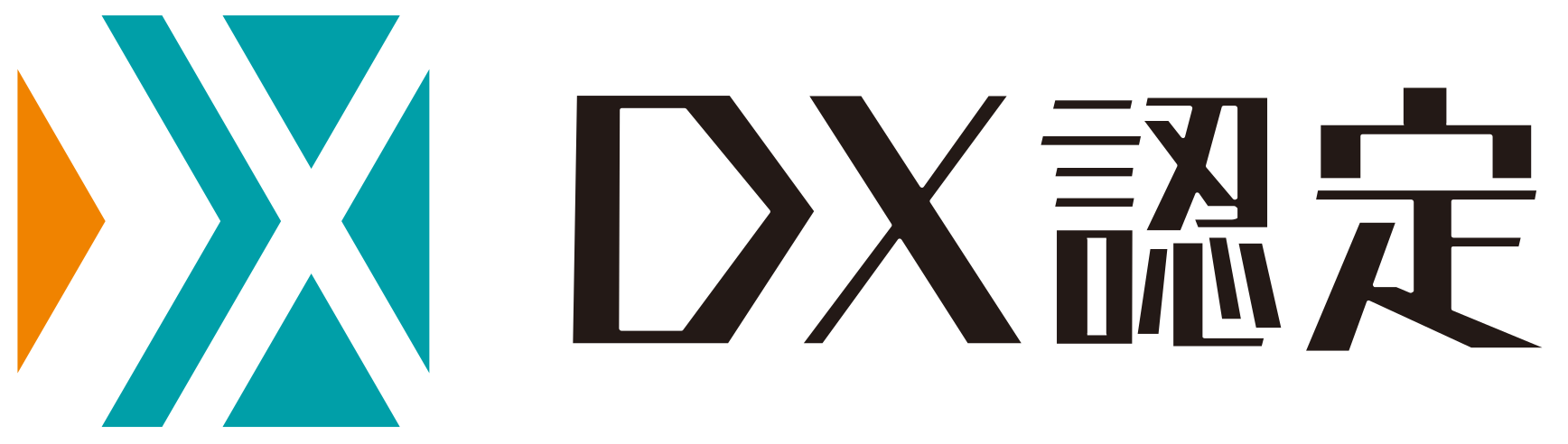
デービー精工は2023年9月1日、経済産業省が定めるDX(デジタルトランスフォーメーション)認定制度に基づき経済産業大臣より「DX認定事業者」としての認定を取得しました。
DX認定制度とは、「情報処理の促進に関する法律」に基づき、「デジタルガバナンス・コード」の基本的事項に対応する企業を国が認定する制度です。経営ビジョンの策定や、DX戦略の実現に向けた体制の整備等を行い、ステークホルダーとの対話を通じて、デジタル変革を進めデジタルガバナンスを向上していく準備が整っている(DX-Ready)事業者を経済産業大臣により認定されます。
デービー精工は、全社標準となるIT基盤(ネットワーク構築、クラウド対応、各データ連携基盤、情報セキュリティ等)の構築を行い、全社標準となるIT基盤を基に3つの指標を掲げ、それらの達成に向けて取り組んでおります。
- 経営体質強化による事業拡大
コア技術とデジタル技術の両技術を融合させ、新たなビジネスモデル創出への取り組み - 高品質/高生産性による企業価値の向上
MES(製造実行システム)の構築及び、基幹システムをベースにSCM(サプライチェーン・マネージメント)の標準化への取り組み - 業務プロセス改善・標準化による業務効率改善/ワークエンゲージメントの向上
全従業員が改革の実感ができる事務系システムの整理及び構築への取り組み
デービー精工は、業務変革や風土変革に向けて、DXを推進していきます。
デービー精工でのDX活動の取り組み
私たちをとりまく事業環境は、持続可能な社会の実現に向けた世界的取り組みに伴う「製品ニーズの変化」、少子高齢化による「労働人口の減少」、労働者の価値観の変化や在宅勤務等による「業務形態の多様性」等、急速に変化しております。これらの事業環境変化に迅速に対応する為には、デジタル技術の活用による業務改革、生産性向上が必要不可欠となります。デービー精工はDXを積極的に推進し、従来のモノづくりを革新していきます。
デービー精工は、コア技術とデジタル技術の融合でイノベーションを創出し、新たなビジネスモデルとして、高品質・高生産性による企業価値向上はもちろんの事、お客先のビジネスが競争優位となるよう取り組んでまいります。又、全従業員が業務効率の改善/働き方改革が実感できる企業を目指しています。
中長期ビジョン
DXの取り組みを通じ、技術と共創の総合力で社内業務に高い評価をもたらす全社標準基盤を構築し、業務効率改善、生産性向上等により、経営体質を強化すると共に企業価値を高め企業サステナビリティに取り組んでいきます。
指標
標準IT基盤をベースに、DX戦略達成指標として下記3点を掲げております。
DX推進体制
デービー精工は、2019年6月に「DX推進プロジェクトグループ」を発足しました。2020年4月からは、事業環境変化に迅速且つ柔軟に対応すべく、社長自らがプロジェクトリーダーとなり全社一丸となったDX活動を推進してまいりました。2023年4月には、当社のDXの方向性と取り組むべきアイテムが整理できた事により、DX推進プロジュクトグループからDX推進部に組織を変更し、DXを推進しております。
本DX推進部は、全社標準となるIT基盤を構築する「情報基盤グループ」、事務所系のシステムを整理・構築する「生産システム1グループ」、MES(製造実行システム)を構築する「生産システム2グループ」、統合型基幹システムをベースとしたSCM(サプライチェーン・マネージメント)の標準化を推進する「生産管理標準化グループ」の4グループで編成しております。各グループには、各部門の代表者を参画させる事により、部門間の連携強化と各部門でのITリテラシーの向上/IT人材の育成を図っていきます。
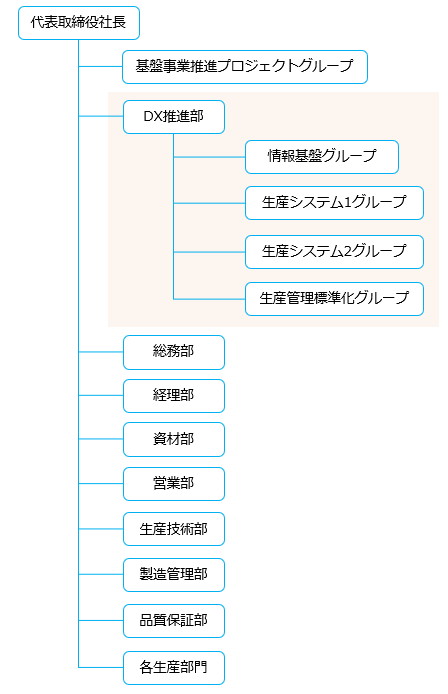
デジタル技術活用の環境整備
IT技術、デジタル技術はめまぐるしく進化しております。システムのレガシー化を防ぐには、技術進化に合わせて管理・更新が可能な「将来に渡って活用できる標準IT基盤の構築」が必要不可欠となります。デービー精工では、全社標準となる標準IT基盤の構築を進めております。
取り組み内容
DXの具体的な取り組み
業務効率改善
2014年にERP(統合型基幹システム)を導入すると共に、各種システム間のデータ連携等にRPAを積極的に活用し、業務の自働化、効率化、正確性向上、コスト削減を図っております。また、バックオフィススタッフにはシンクライアントPCを配付し、電子ワークフロー(電子承認)の導入や、社内外とのWEB会議、在宅勤務等、業務効率の改善と働き方改革に向けて取り組んでおります。
生産性向上 ~MES(製造実行システム)構築~
自社で製造設備のPLCから設備稼働状況を収集するシステムを開発しました。このシステムでは、時間出来高、不良情報、トラブル情報の取得が可能であり、これらの情報を活用し改善PDCAを行う事により生産性向上を図っていきます。21年3月より導入を開始し、24年度末までに、社内の主要な製造ラインへの導入が完了しました。
改善効果
- 設備稼働状況の把握による生産ロス低減
- 不良データの集計、傾向管理、分析による品質改善
- チョコ停等トラブルデータの見える化による設備改善ポイントの明確化
- 前工程の終了ログ自動確認による工程飛び防止
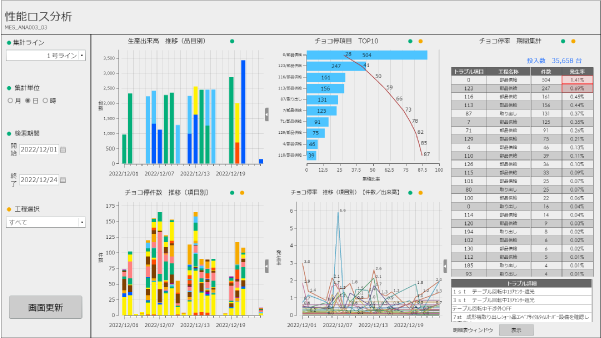
DXの将来構想
事務所系システムと生産現場系システムそれぞれのデータベースを整理すると共に情報を有効活用する為のデータ連携基盤を構築し、データドリブン思想に基づき、さらなるPDCAサイクルの高速化を推進していきます。
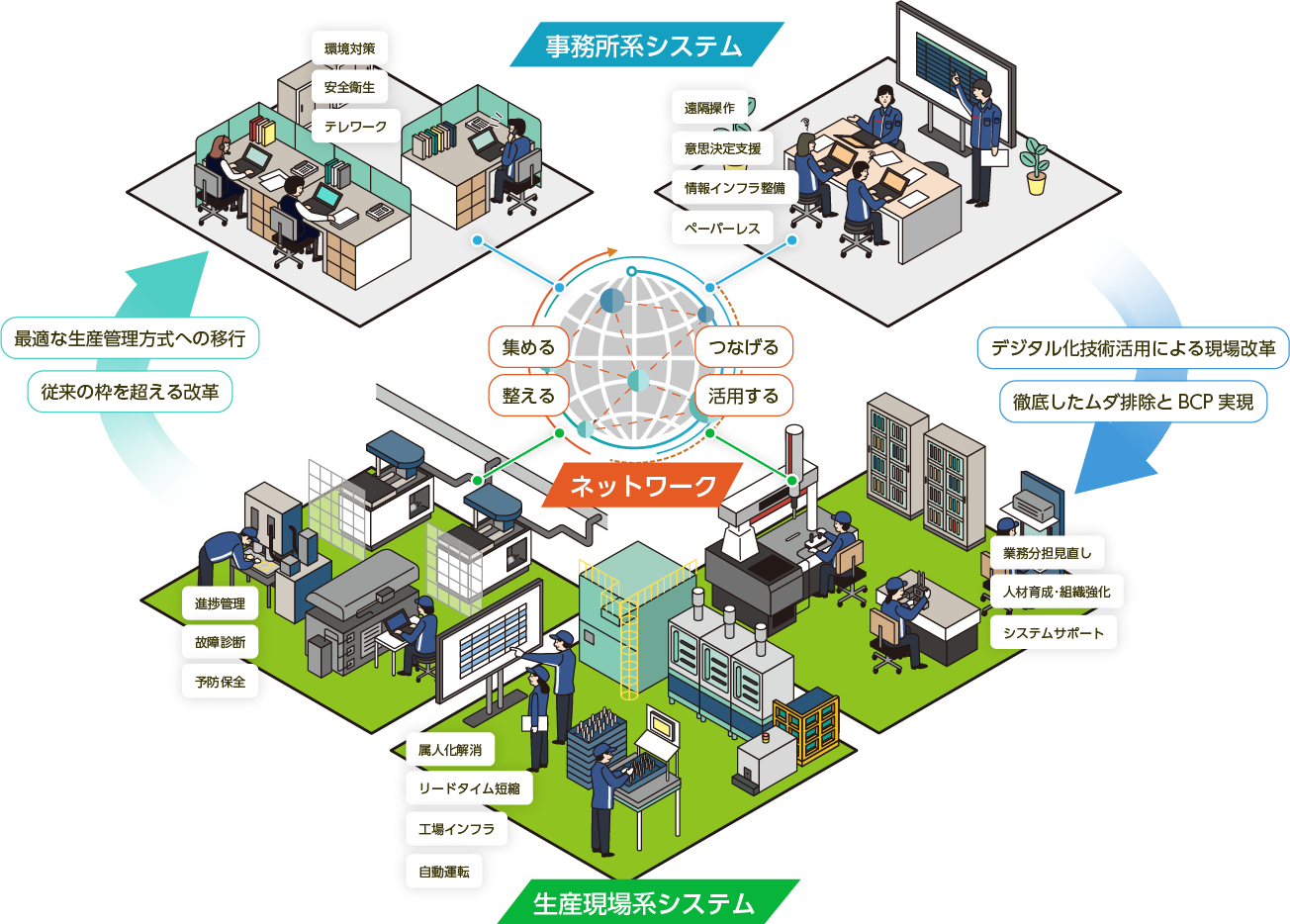
お問い合わせは下記のお問い合わせページより、
お気軽にどうぞ!