技術力
保有技術

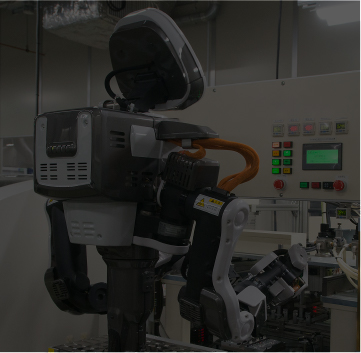
長年にわたって築き上げ、蓄積してきた技術
さらに磨き上げ、向上させる技術
製造要素技術
新たな飛躍を目指す
工程設計
製品情報や生産計画を基に生産設備や作業員配置を構想し、製品完成までの一連の加工プロセスを設計します。この段階で投資額や原価・利益率がほぼ決定するため極めて重要な業務です。
要素技術
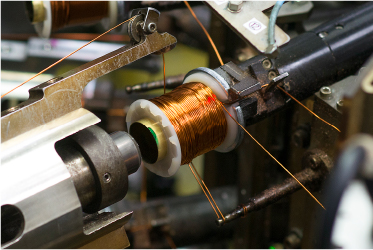
巻線巻線は、ボビンと呼ばれる部品等に電線を巻き付ける工法です。デービー精工では、0.06mmから2.7mmの線径を扱っています。
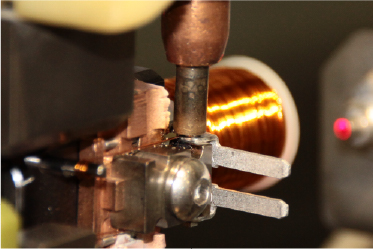
ヒュージングヒュージングは、電気抵抗を利用して熱カシメ(拡散接合)を行う工法です。巻線の端末処理に活用しており、主にフック形状の加工を行っています。最適な条件を見出し管理しています。
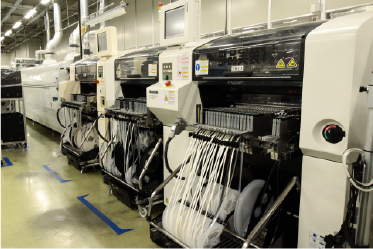
SMTSMT(Surface Mount Technology)は、表面実装と呼ばれる基板実装工法です。基板の表面に設けられたパッドに電子部品の電極を接合します。主にはんだ印刷→電子部品マウント→リフローはんだ付けで構成され、はんだ付け部の品質保証のため画像検査も導入しています。
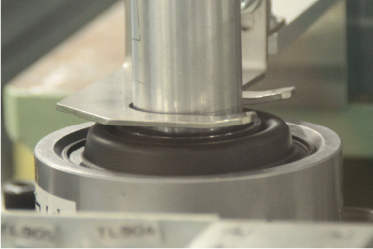
超音波溶着超音波溶着は、超音波振動と加圧力によって、樹脂同士の接合面に強力な摩擦熱を発生させ、樹脂を溶融し接合させる工法です。また、加工時間が短いことが特徴です。気密性を求められる製品に採用しています。
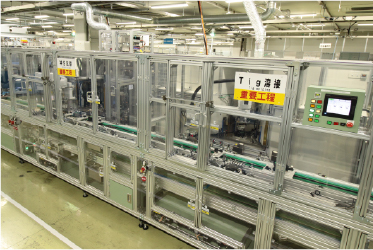
自動化技術製品の組立・加工・検査・運搬等、人による作業をロボットやアクチュエータ、各種センサを応用し設備に置き換えます。これにより生産効率向上や安定した品質を確保できます。また近年ではデジタル技術(AIやIoT等)を応用し更なる生産性向上を目指しています。
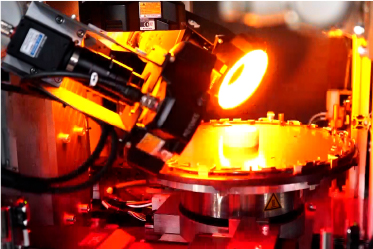
画像検査複数のカメラをロボットに搭載し、検査対象に合わせて、カメラの位置や角度を変えて人のように検査します。複数箇所を同時に検査することにより、検査時間の短縮と省人化、高精度かつ一定品質で検査を実現しています。
デービー精工が保有している要素技術!!
- 巻線
- フライヤ―巻線
- スピンドル巻線
- 接合技術
- 溶接
- TIG溶接
- 抵抗溶接
- レーザー溶接
- カシメ
- ヒュージング
- ローリングカシメ
- ハイスピンカシメ
- はんだ付
- ロボットを使ったコテはんだ付け
- フローはんだ
- 部分噴流はんだ
- 圧入
- 自動ネジ締め
- 接着
- 超音波溶着
- ロウ付け
- 溶接
- 金属プレス加工
- プラスチック射出成形
- SMT(表面実装)
- 試験・検査
- 画像検査
- 空圧・油圧試験
- 電気試験
- 印字、マーキング
- エポキシ封止、ポッティング
- 洗浄
設備技術
製品の生産設備の構想、仕様検討から保守管理まで自社のエンジニアが行います。また、モノづくりの基盤となる様々な要素技術を用いた設備を検証し量産化に向けた生産ラインの立ち上げ、量産後の改善など生産性や品質向上を常に意識しています。
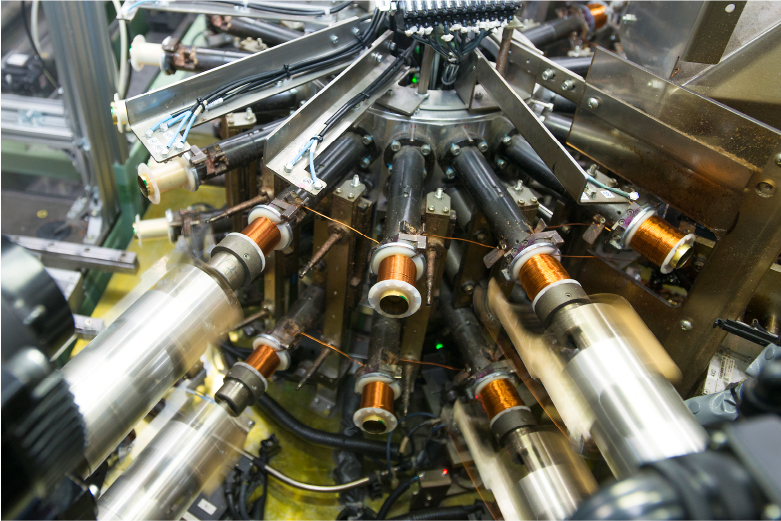
金型設計・製作
量産性を考慮した生産設計の提案ができます!
金型設計
最適な歩留検討だけでなく、品質・生産性を考慮した製品形状の改善提案を行います。
また、具体的な金型設計では、設計者、部品加工者、金型製作者、金型メンテナンス者、プレス加工現場からの意見を出しあって、年間約50面製作する新規金型すべてに対してデザインレビューを行い、量産性の良い金型設計に取り組んでいます。3D
CADの活用により設計業務の効率化に取り組んでいます。
部品加工
金型を製作するための加工機を自社で保有し、新規金型の部品だけでなく、メンテナンス用部品の製作も行います。
それぞれの加工機について国家技能検定の取得を計画的に行い、作業者の技能の向上に取組んでいます。
下記のNC加工機に加えて旋盤、フライス盤等の汎用設備も揃えています。
加工機
- ワイヤ放電加工機
- 形彫放電加工機
- プロファイル研削盤
- マシニングセンタ
- 平面研削盤
- 成形研削盤
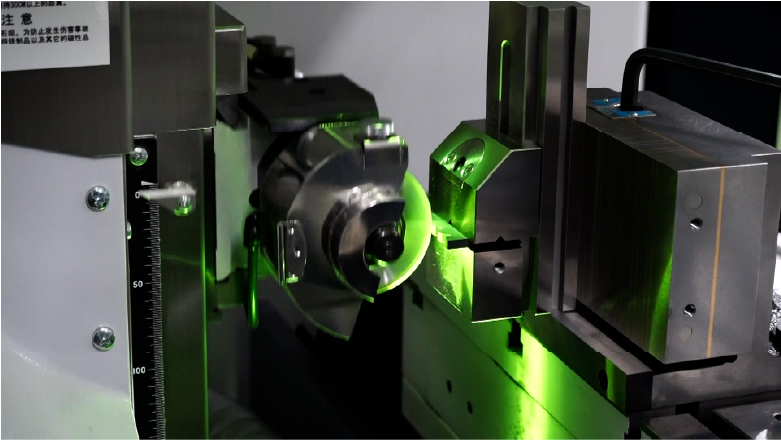
金型組立
製作された金型部品を一つ一つの部品について細かく勘合状態を確認し、熟練の作業者の手で仕上の調整を行い、高精度な金型を製作します。
メンテナンス
定期的に金型メンテナンスを行うことで、製品出来栄えが常に一定となるように金型を管理しています。
さらに突発的なトラブルでも、自社保有の加工機を最大限に活用して最短時間で復旧が可能です。
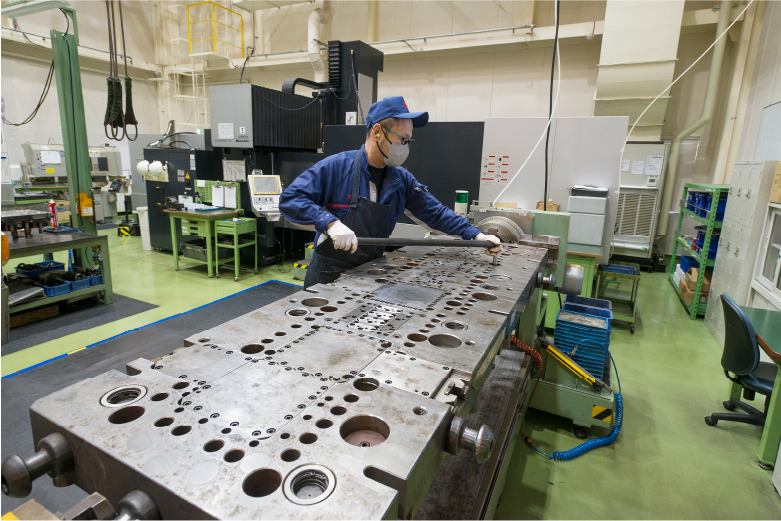
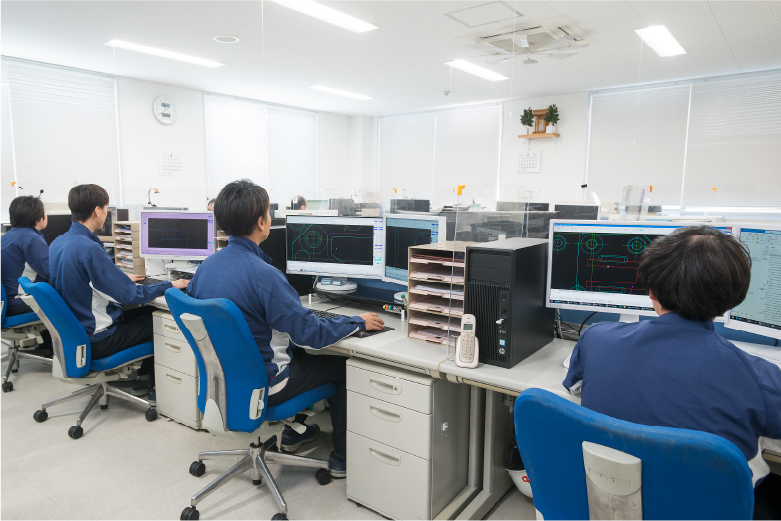
設備設計・製作
一から、機械設計やソフト設計、さらに機械・電気組立まで自社対応できます!
機械設計
設備ごとに新しい技術や工夫を取り入れ、仕様、安全、品質、作業性、適正なサイクルタイムを満足する設備設計を行っています。
設備仕様立案、設備構想、組立図設計、部品図設計まで一貫して取り組んでいます。
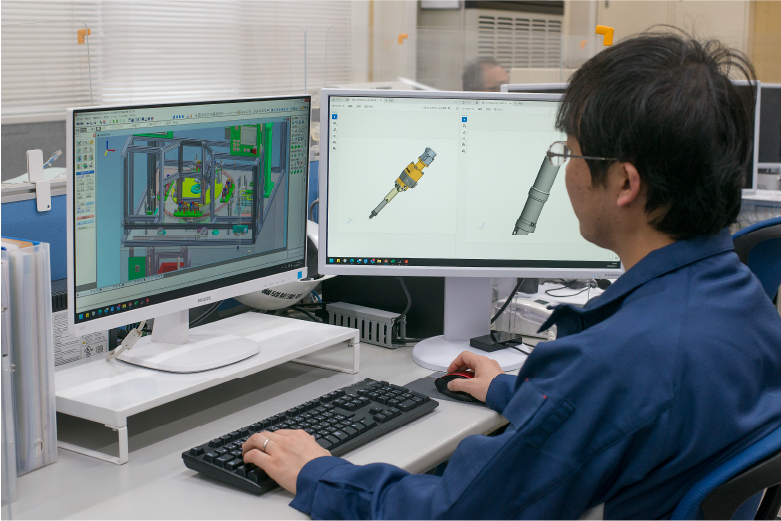
電気設計(ハード・ソフト)
配線図や制御盤図といったハード設計と、プログラムや操作インターフェイスなどのソフト設計の両方を行っています。
何より安全に使ってもらえるよう、シンプルでわかりやすい回路設計を心がけています。
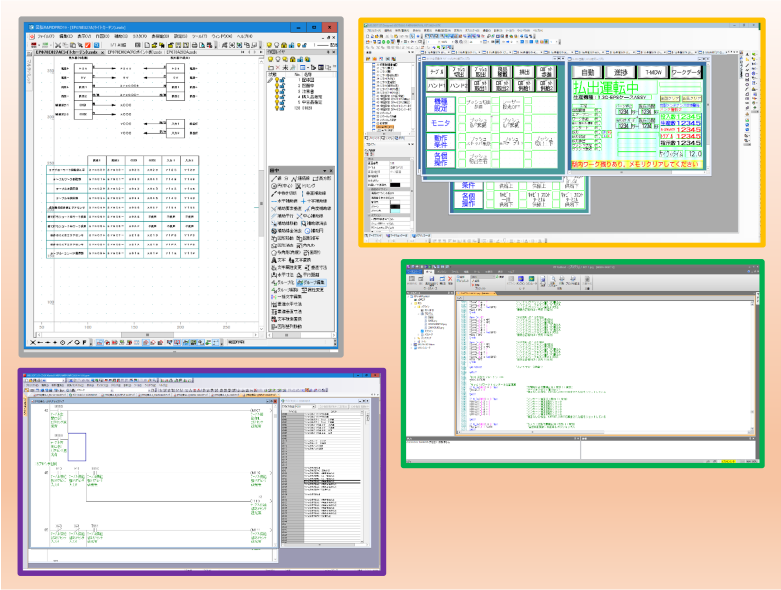
機械・電気組立
設備組立時に精度測定を行い、測定結果を設備調整に反映させ、高い精度が必要となる自動車部品製造のニーズに対応しています。
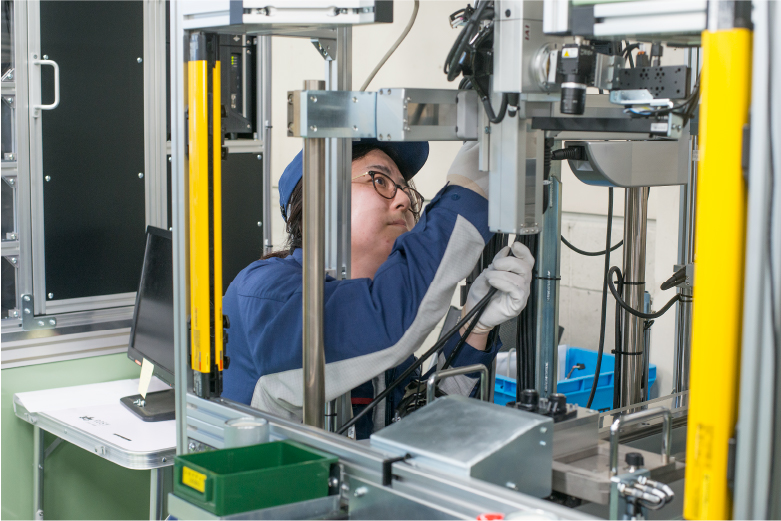
新しい技術への挑戦
これまでに、
- 協働ロボット(双腕ロボット)を使用した作業者負荷低減を目指した設備製作
- ロボットと画像センサを組み合わせたランダムピッキングの技術確立
- 成形金型への部品インサートで金型位置ずれを自動で補正する技術確立
これからは、合理化や省人化を目的にAIの活用等、新しい技術に挑戦していきます。
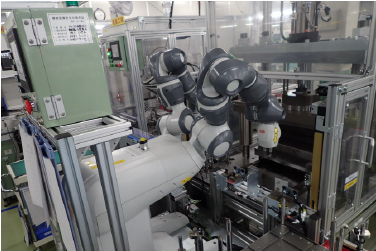
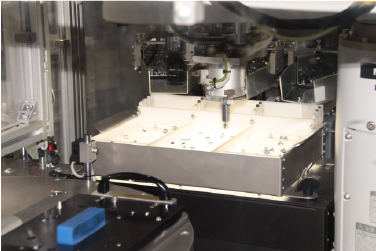
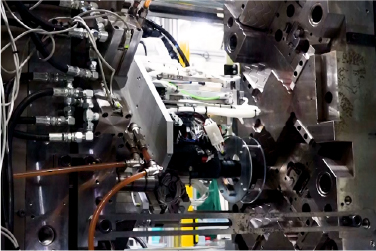
全社教育
全社の設備技術の向上を目的に、社内講習を実施しています。
- 設備基礎知識
- 基礎シーケンス制御
- 国家技能検定電気系保全
等
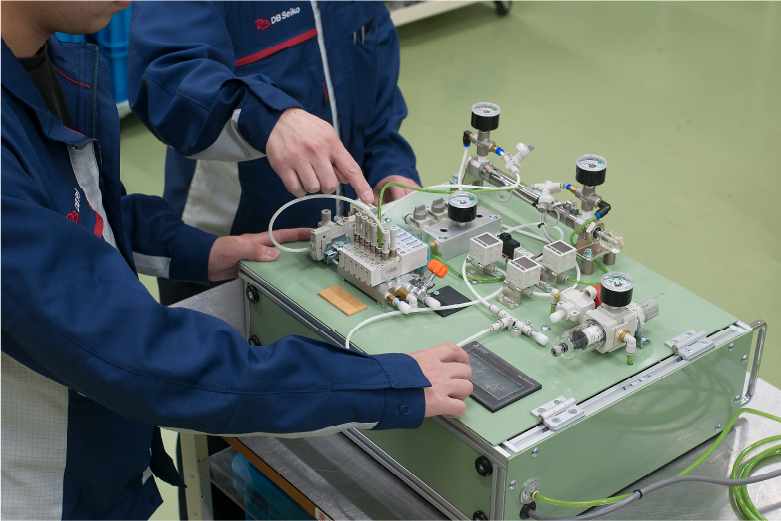
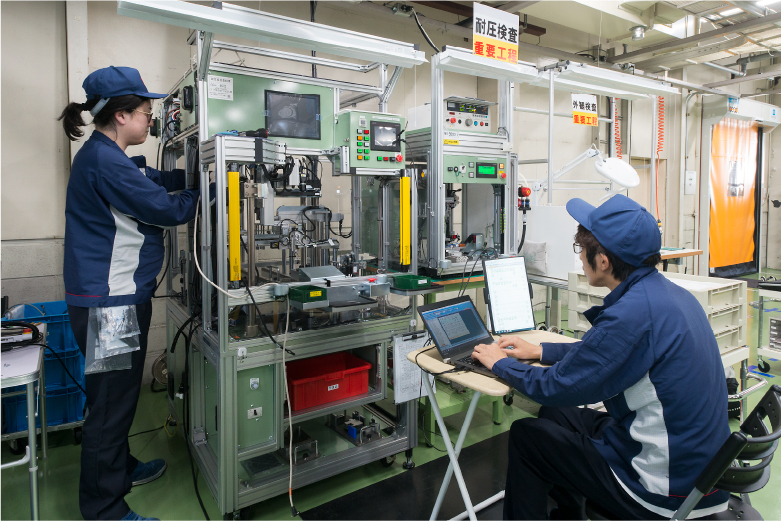
精密プレス加工
精密プレス加工へのこだわりがあります!
カス噛みセンサ取付により品質を維持し、荷重センサ取付により金型と設備の状態監視を行っています。騒音の大きな設備には防音ボックスを設置し、作業環境と安全に配慮しています。
技術面では、今後ますます需要の増加が見込まれるモータ用部品のプレス加工技術の向上に取組んでいます。また、より精密な端子、バスバー製品製作の為、プレス機及び金型精度の向上、カメラによる自動検査の導入等、新たな技術にもどんどん挑戦しています。
保有プレス機 | 加工 |
---|---|
110~300t
|
絞り、曲げ、バスバー、精密端子抜き |
80~300t
|
積層製品、端子部品 (量産実績:最大600spm) |
※右方向にスクロールできます
フープ材質
- SPCC
- アルミ材料
- 銅材料
- 電磁鋼板
板厚
- 0.3~3.2mm
製品の取出しには、ロボットによる自動取出しやパレタイザ等の技術を使い、省人化を図っています。
設備データの可視化により、事後分析や生産管理の活動を行っています。
プレス加工の建屋全館、空調制御により材料と金型、設備の温度を一定に保ち精密プレス加工を可能にしています。さらに、建屋内は土足禁止や定期的な清掃等を実施し、美しい製造現場を維持できるよう管理しています。
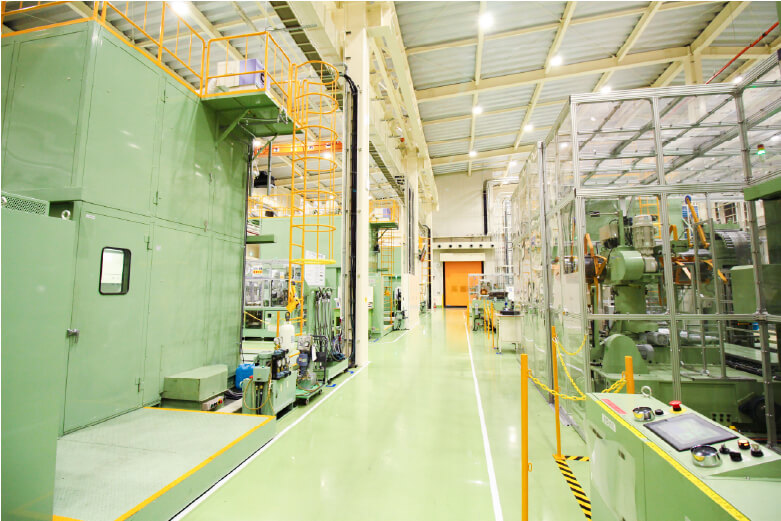
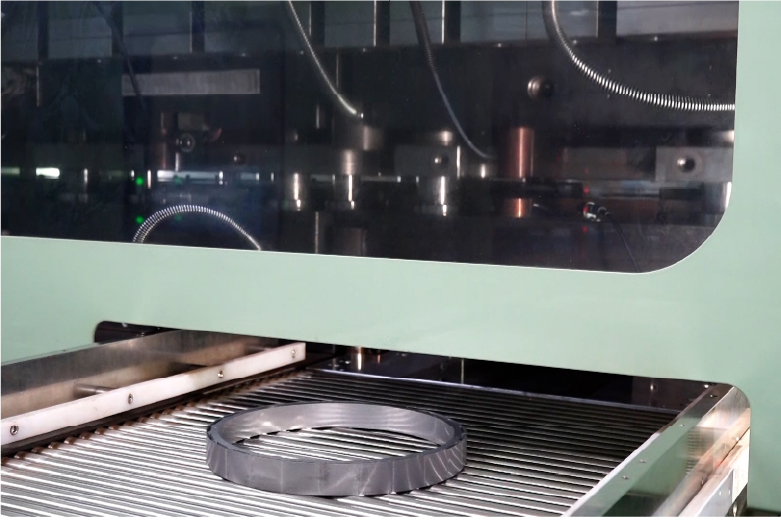
プラスチック射出成形
自動化による成形作業の省人化
最新機器を活用した解析・分析
保有設備・主な取扱樹脂
約100台の射出成形機を保有しています。
主な取扱樹脂はPA66、PBT、PPSで、ガラス繊維強化エンジニアリングプラスチックが主体となっています。
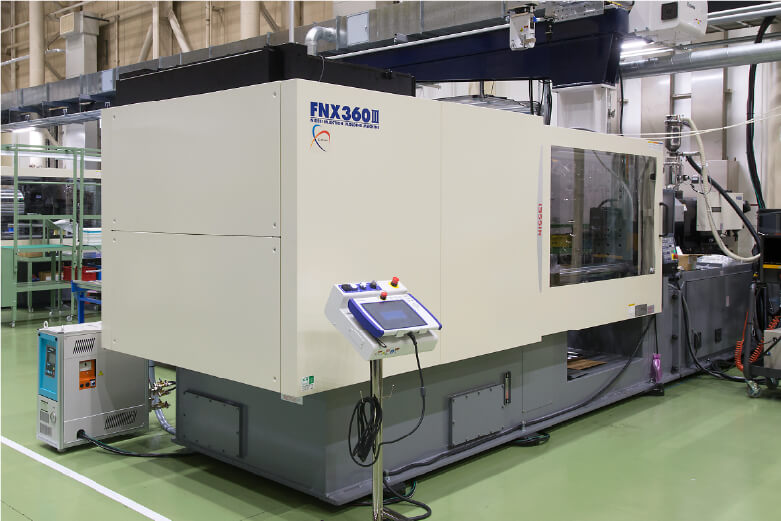
自動インサート成形による省人化
ロボットによる、自動インサート成形を行っています。
省人化、インサート時間短縮に取り組みます。
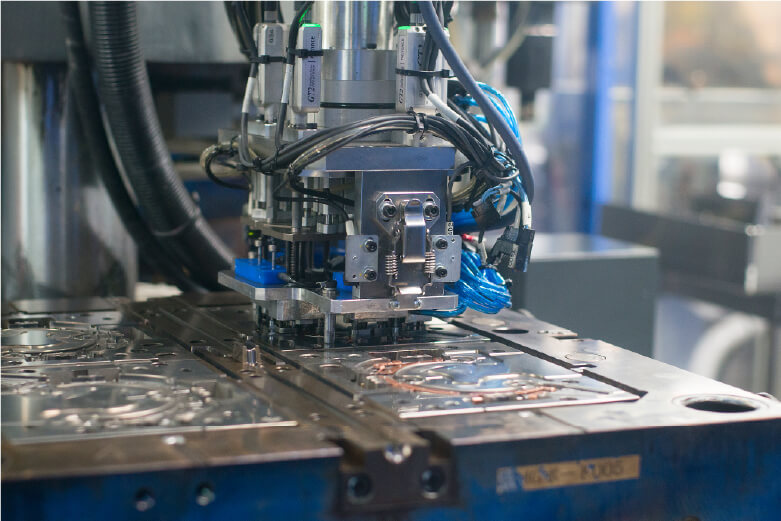
解析・分析
3D CADの導入による金型DR(デザインレビュー)を行うことで、コストダウンと品質の向上を目指します。
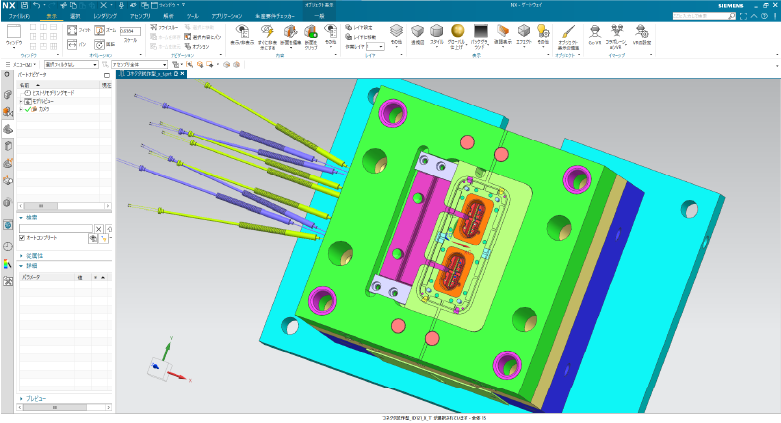
3Dスキャナ型三次元測定機
成形品の形状を測定し、製品図面と比較します。
測定結果を金型に反映します。
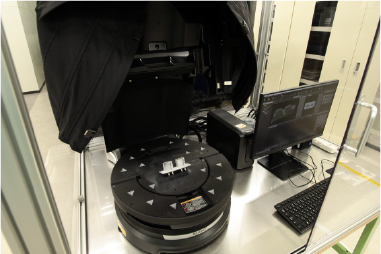
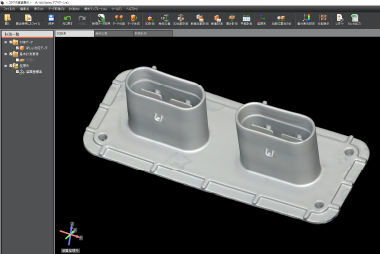
メルトインデックサを導入
樹脂の流動性を監視し、成形不具合を未然に防ぎます。
プラスチック成形技術向上
試験金型を製作し、温度センサにより冷却効率や圧力センサによる圧力波形を確認することで、成形技術の向上を図っています。
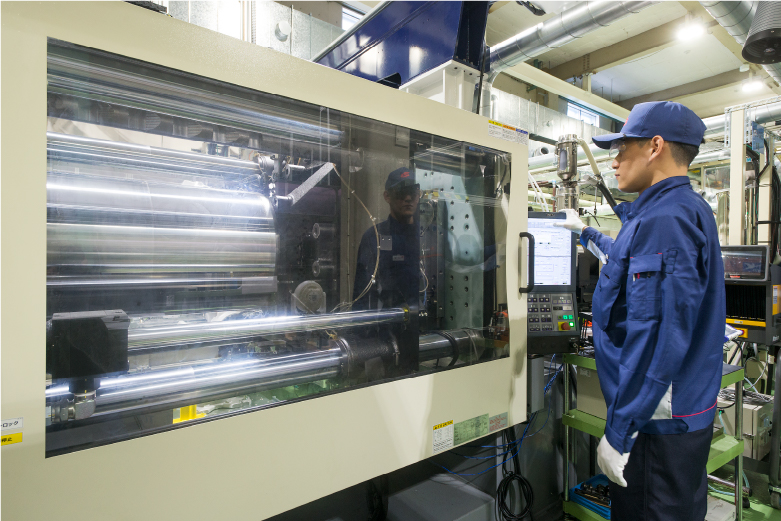
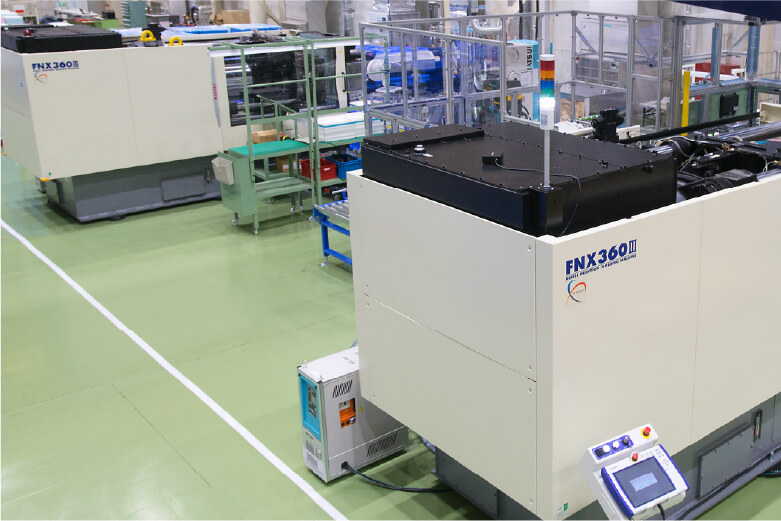
品質管理
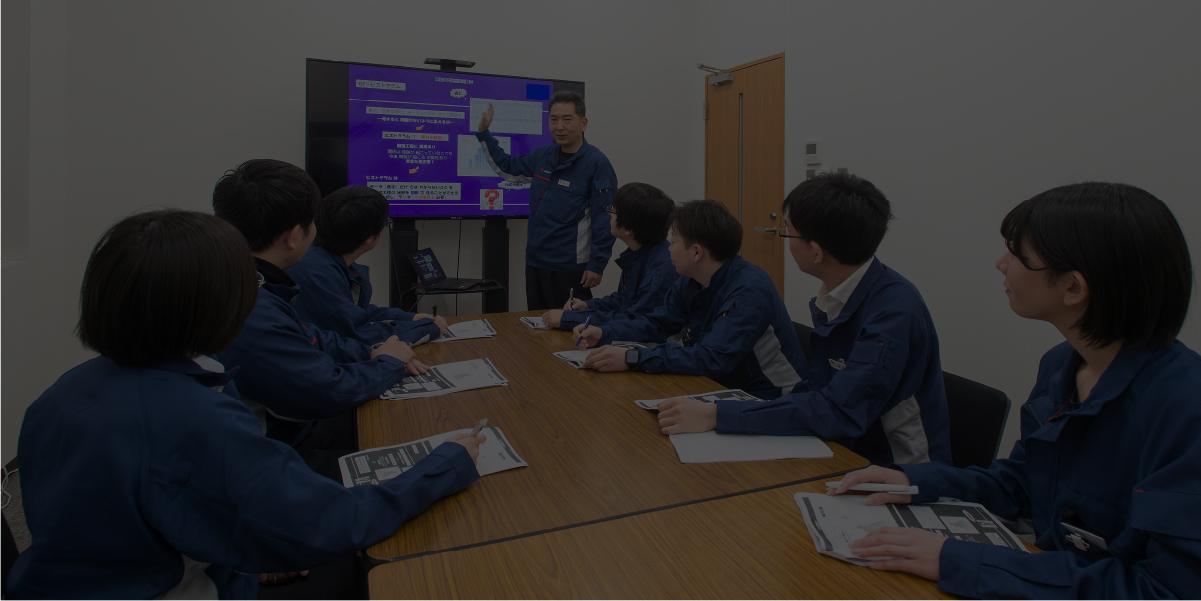
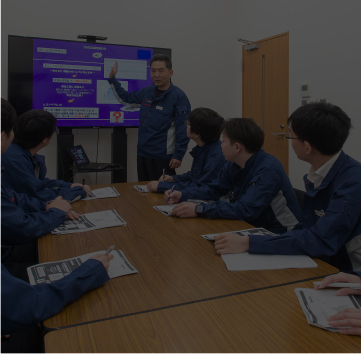
自動車産業の国際規格IATF16949認証取得メーカです。
製造工程の徹底した品質管理、厳しい製品検査、不具合モードの解析や素材の分析、及び、人材育成により自動車部品に求められる高い品質レベルを獲得しています。
計測技術
最新の3D画像測定器や三次元測定機による自動測定技術と検査員の熟練した計測技能の融合により、製品を高精度でスピーディーに検査し、高品質の製品をお客様に提供しています。
また、技能検定の受講により、機械検査技能士の国家資格取得、測定プログラミングや測定技術の社内研修を開催し、測定技能者の育成にも積極的に取り組んでいます。
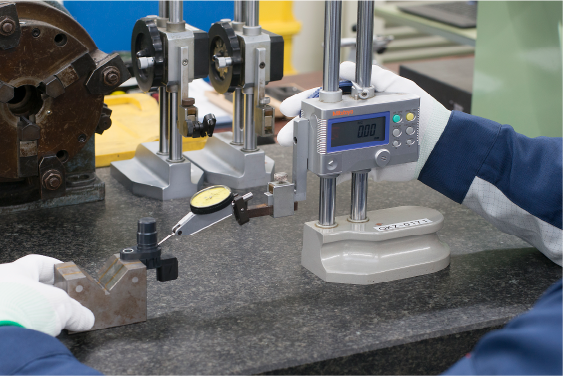
主要測定機
- 画像測定器
- 三次元測定機
- 形状測定機
- 工具顕微鏡
- 万能試験機
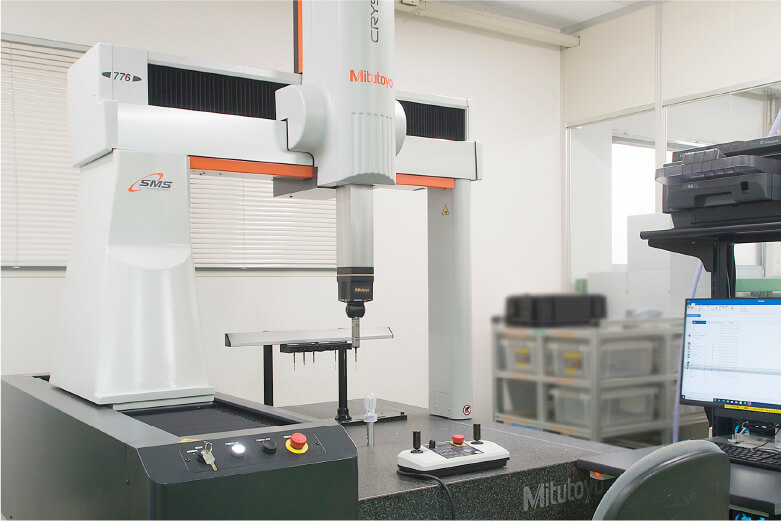
解析技術
走査電子顕微鏡(SEM)による銅線の破断面観察、マイクロスコープでの焼き入れ品の金属組織観察・鍛造製品のファイバーフロー評価、FT-IRを用いた樹脂材料の分子構造評価などによる不具合モードの解析や素材の品質確認を実施しています。
分析例
- 走査電子顕微鏡(SEM)写真(銅線破断面)
- マイクロスコープ写真(焼き入れされた金属組織)
- FT-IR波形(樹脂の波形比較)
走査電子顕微鏡(SEM)写真(銅線破断面)
マイクロスコープ写真(焼き入れされた金属組織)
FT-IR波形(樹脂の波形比較)
主要分析装置
- 走査電子顕微鏡(SEM)
- エネルギー分散型X線分析装置(EDS)
- マイクロスコープ
- 蛍光X線膜厚計
- FT-IR
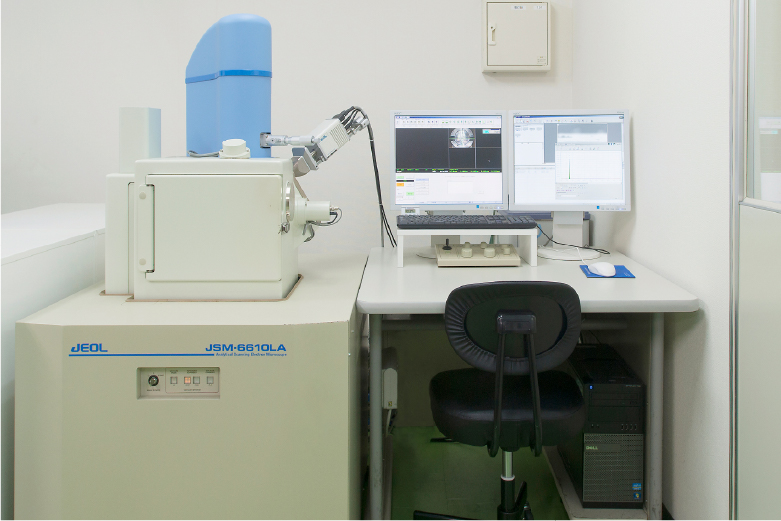
品質管理教育
新入社員、中途採用、ベテランなど様々な階層の社員に対して品質講習を実施し、品質管理の基礎から高度な統計的管理手法に至る種々の知識を身に付ける教育活動を活発に展開しています。
主要講習
- 品質管理基礎講座
- APQP(先行製品品質計画)講座
- PPAP(生産部品承認プロセス)講座
- FMEA(故障モード影響解析)講座
- MSA(測定システム解析)講座
- SPC(統計的工程管理)講座
- IATF16949要求事項講座
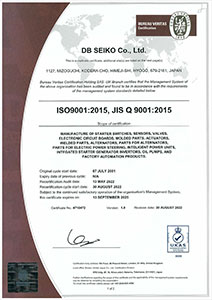
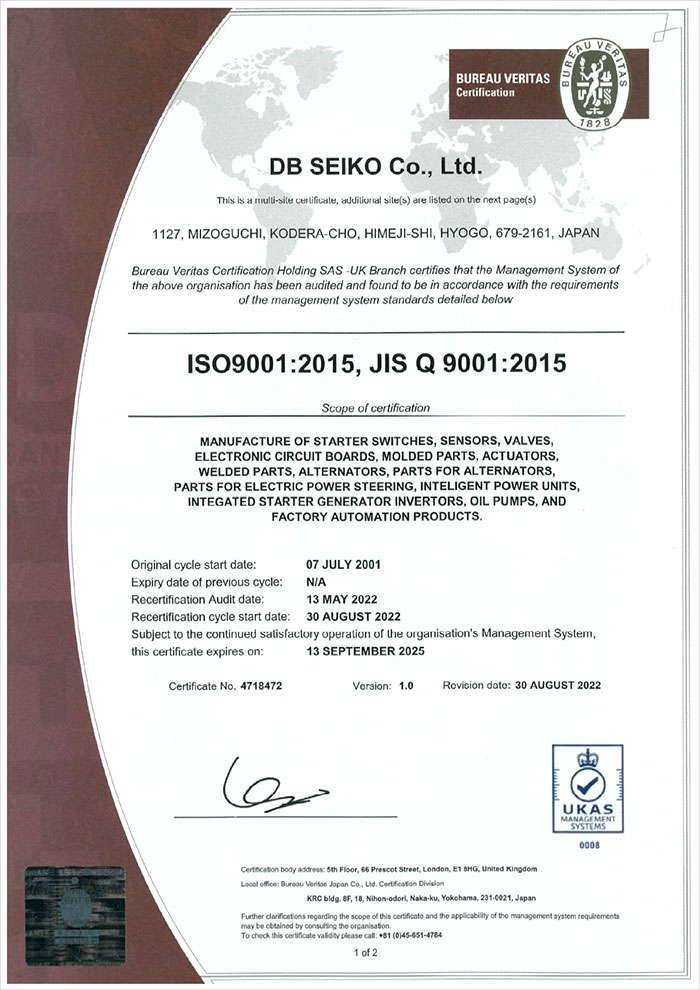
ISO9001(2015)
取得年月:2001年07月
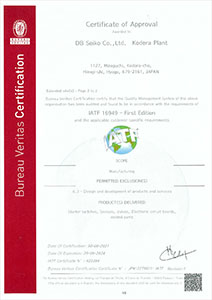
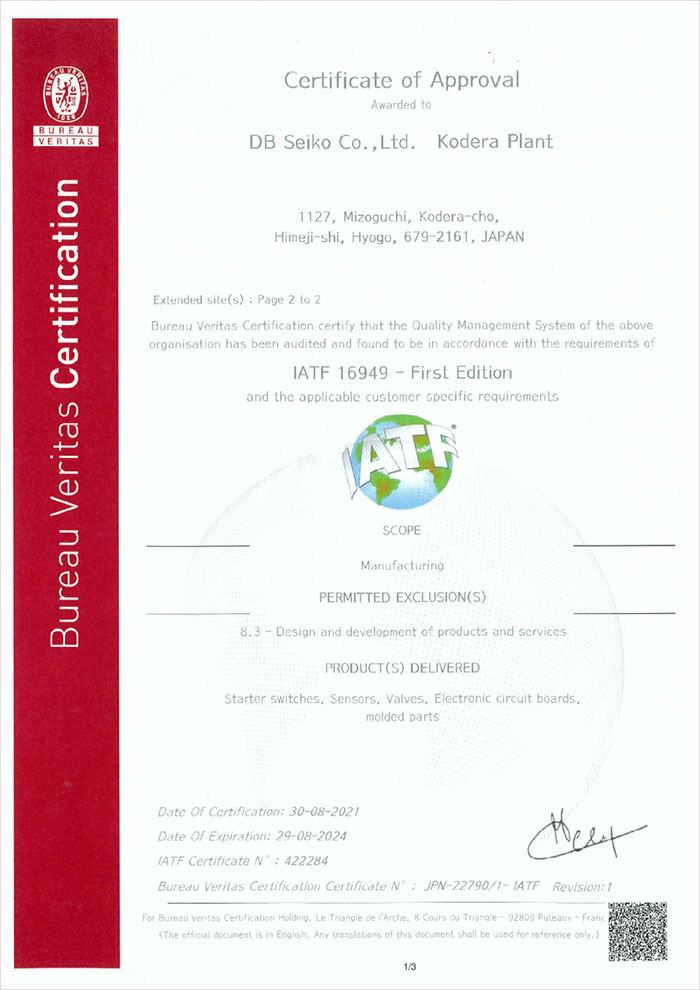
IATF16949
取得年月:2018年8月
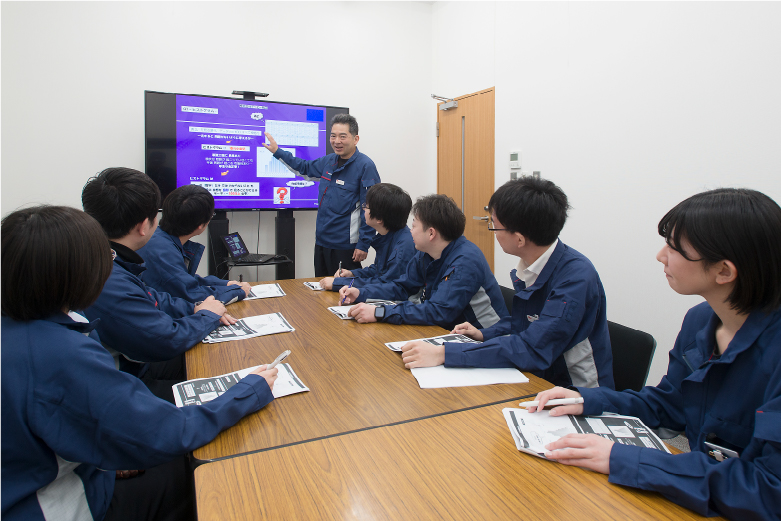
お問い合わせは下記のお問い合わせページより、
お気軽にどうぞ!